「海洋大学でなぜチタンの研究をするのか?」
主な理由は私がただ興味があるからです。酸素がどのような影響を与えているか,どこまで酸素が使えるか知りたいです。耐食性が高く,意匠性(見た目)がいいので,海水環境で使用できます。しかしコストが高いため,汎用材として利用するには精錬技術の技術開発が必要です。
課題であるチタンの低コスト化
チタンおよびチタン合金の製造量は、航空宇宙関連事業から地球温暖化防止(CO2排出量削減、燃費向上)を目指した自動車用部品、チタン特有の耐食性や意匠性を利用した滑走路等の海洋構造物からの需要で2009年から2012年まで急激な伸びを示していました(図1)。しかし,世界的に低下傾向ではあるものの日本での生産量は急激に低下しています。これは、二酸化チタン(TiO2)を高純度チタンへと還元する際に電力を大量消費するので,2010年から東日本大震災以降の2014年までで電気料金が25%上昇した近年の日本の電力事情の中ではコスト面で厳しくなったことが大きな要因の1つです6)。そのため,チタン創製の低コスト化に向けた技術開発が重要となっています。これまでにも新規還元プロセスの確立、加工コストの低減と低コスト元素合金設計の確立に向けた研究がなされてきました。特に,チタンの還元プロセスで問題視される侵入型元素(酸素O,鉄Fe,窒素N)をチタン・チタン合金の合金元素として組織設計する試みがなされており、バナジウムVやモリブデンMoを多く添加したβ型チタン合金(bcc構造)では侵入型元素を有効利用できる例が報告されています5) 。一方で,α型チタン合金(hcp構造)では有効利用に関する研究は少ないです。
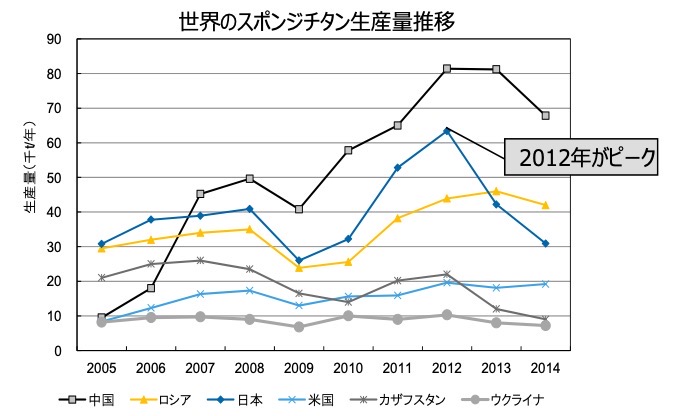
図1 スポンジチタンの生産量推移1)
酸素を合金元素とすることによる低コスト化の方法とそのメリット
チタンの還元プロセスは工程数が多く(表1),バッチプロセスであるため高純度のチタン材を創製するのにはコストがかかります。還元プロセスを経て創製された純度の高いポーラス状のチタン(スポンジチタン)は,真空中でアーク溶解し鋳造することにより純チタン・チタン合金のインゴットとして創製されています。この還元プロセスにおいて純度を限りなく高めるのではなく酸素を残存させることで酸素を有効利用する試みをしています。運用面での管理も容易です。また,創製した純チタンと二酸化チタン(TiO2)を混ぜて鋳造することによりスポンジチタンの量を減らすことができるため,材料費を削減できます。このように酸素を合金元素として有効利用できればコスト低減に繋がります。酸素は資源的な制限がほとんど無い上に固溶強化能が高く、材料比重も変化させない利点を有するので4)、チタン中の酸素の役割を明確化することは工業的にも学術的にも有意義です。
表1 チタンの還元プロセス
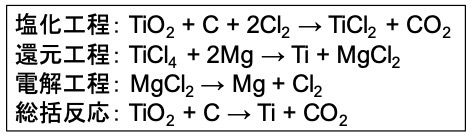
酸素量と延性
上記の背景から様々な研究者によりチタンおよびチタン合金への合金元素として酸素を有効利用する試みがなされてきていましたが4),酸素固溶量>0.5mass%ではあまり検討されていませんでした。これは酸素固溶量>0.50%では1949年のJaffeeらの報告1)で延性を示さないことが示され,脆性的であると信じられているためです。本研究室では酸素固溶量>0.5mass%でも異方性を制御することで,高い延性を得られることを発見しました(図1)。そして,異方性を制御したTi-O合金(方向性Ti-O合金)の力学特性とその変形機構を明らかにし、集合組織を発達したTi-0.71mass%Oが20%程度の全伸びを示し,集合組織制御によりOを合金元素として有効利用できる固溶量の範囲を拡張できる可能性を見出しました。(この研究は横浜国立大学 梅澤修教授と共同で行っています。)
図1 開発Ti-O合金の酸素量と伸びの関係
参考文献
1) R.I. Jaffee and I.E. Campbell: Metals Trans.: 185(1949), 646-653.
2) Y. Murayama, M. Mikami, N. Ishiyama, and S. Hanada: J. Japan Inst. Metals, 57(1993), 628-636.
3) W.L. Finlay and J.A. Snyder: Trans. AIME, 188(1950), 277-286.
4) C. Ouchi, H. Izumi, and S. Mitao: Mater. Sci. Eng., A243(1998), 186-195.
5) T. Ando, S. Tuchiyama, and S. Takaki: J. Japan, Inst. Metals, 72(2008), 949-954.
6) 経済産業省:2030年を見据えた非鉄金属材料の戦略(2016).
7) M. Niinomi: J. Japan. Inst. Metals, 75(2011), 21-28.
8) 刈屋翔太,梅田純子,Ma Qian,近藤勝義:日本金属学会誌, 82(2018), 390-395.